Abstract
A unique gas density meter that is compatible with light gases at low pressures now available. Gas density and concentration test data over pressure for air, hydrogen, nitrogen, argon, methane, carbon dioxide, sulfur hexafluoride and gas mixtures are presented in this white paper. The measurement of hydrogen density at low pressure (101KPa to 400KPa) is demonstrated. Coupling binary gas concentration and density measurements of low pressure, light gases like hydrogen, natural gas and methane opens up new sensing applications like fuel cells, energy management, chemical and semiconductor processing.
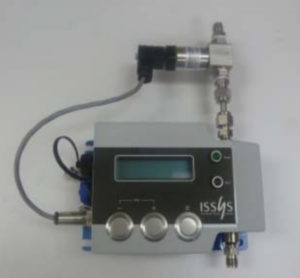
Fig. 1. The density meter (bottom) and pressure sensor (top).
Introduction
A number of gas concentration sensors have been developed and include thin film electrochemical, infrared [1], metal oxide semiconductor [2,3], acoustic [4,5] and ultrasonic [6]. While some can resolve part per million concentration differences there have been problems with hysteresis, selectivity, drift, cross sensitivity.
Steel [7-10], glass and even micromachined silicon [11-12] resonating tubes have been used to measure density and mass flow of liquids and highly compressed gases via the Coriolis effect [7-10]. Unlike steel tube meters which are fabricated one at a time; MEMS-based sensors employ wafer fabrication enables hundreds of micromachined silicon Coriolis mass flow tubes and even assembled subsystems to be produced with one wafer stack. This batch fabrication method reduces the manufacturing costs enabling a wider use of density sensor technology. This paper shows how ISS has developed resonating micromachined silicon tube technology for use in density and binary gas concentration measurements. Special attention is given to light, low pressure gases like hydrogen and nitrogen which have not been measured with conventional metal Coriolis mass flow and density meters due to the high material density and thickness of the metal tubes.
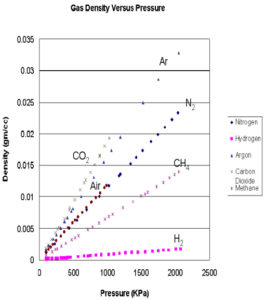
Fig.2. The variation of several light gases.
Test Results
Since gas is a compressible fluid the first step in developing a gas sensor is generally to characterize its performance over pressure. The silicon tube resonant frequency varied with pressure for nitrogen at room temperature. As the pressure increases, the density increases and hence the resonant frequency decreases due to the increase in total mass. A water filled tube will have a resonant frequency of 23.65 KHz, while an air filled tube will have a frequency of 28.7 KHz.
To accurately measure the density of a compressible gas using the frequency of a resonating tube requires knowledge of the gas temperature and pressure, which are related via the ideal gas law. Two options are available; making measurements at a known, fixed pressure or continuously monitoring the pressure of the gas. For this study an absolute capacitive pressure sensor (top) was used in series with the density meter (bottom) as shown in Fig. 1. The pressure sensor output if fed directly into the density meter via a cable. The density sensor was designed as an intrinsically safe device, meaning that the voltage, current and capacitance values were kept low to prevent a flame igniting spark from being generated in case of unforeseen conditions causing shorting of adjacent wires, components or circuit board traces. The density sensor design including the external pressure sensor were certified intrinsically safe (UL, ATEX, Class 1 Div 1) for the industrial environment, enabling them to be utilized for measuring gases like hydrogen and methane. During data gathering an additional pressure sensor was employed on the test stand to insure high pressure accuracy of the measurements.
A number of gas density data plots were generated using both the resonating microtube and capacitive pressure sensor. Compressed gas cylinders, with 4 digits of accuracy using NIST traceable standard, were used in the calibration and testing of the device. All date was taken for these figures at temperatures between 23 and 24°C.
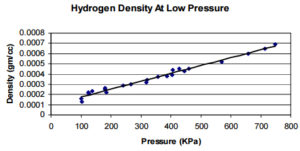
Fig. 3. The variation of hydrogen density with pressure in the range of 101 to 750 KPa.
Fig. 2 gives a pictorial comparison on the density of several light gases versus pressure such as hydrogen, methane, nitrogen, air, argon and carbon dioxide. Fig. 3 expands the low pressure range of hydrogen gas density data. This low pressure region is one of the unique capabilities of this technology. The linear fit for the hydrogen density data, R2 value of 0.9989, closely matches that of the ideal gas reference. The density of silicon is 2.33 gm/cc versus 8 gm/cc for stainless steel or 4.54 gm/cc for titanium. The use of conventional metal tube Coriolis mass flow and density meters have been restricted to relatively high pressures [7-10]. The silicon microtube walls are only a few tens of microns thick versus millimeters thick for conventional metal Coriolis mass flow and density meter tubes. While the measurement of the density of a low pressure light gas like hydrogen is extremely difficult for conventional metal tubes, it can be accomplished using the less dense, micromachined silicon resonating tubes.
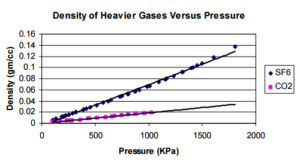
Fig. 4. The density of sulfur hexafluoride and carbon dioxide versus pressure.
It is of industrial interest to measure the density of heavier gases in applications such as semiconductor processing, welding, refrigeration and insulating electrical switches. The fabrication of integrated circuits, MEMS and the MEMS microtubes used in this density sensor utilize sulfur hexafluoride and other gases as an etchants in the deep reactive ion etching or plasma etching processes [13,14]. Fig. 4 plots the density of sulfur hexafluoride SF6 versus pressure. As a comparison the density of carbon dioxide is also plotted on the same graph. Both gases are relatively non ideal at higher pressures due to their molecular complexity and as a result the density variation deviates from linearity at high pressures. It should be noted that the density of liquids with densities ranging from 0.7 to 1.5 gm/cc have been measured with the silicon microtubes of the same dimensions [11,12].
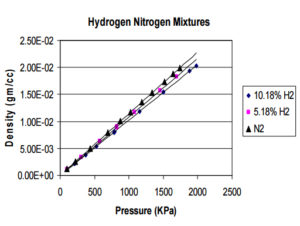
Fig. 5. The variation in gas mixture density with pressure for different nitrogen-hydrogen mixtures.
The density of fluids can be used to determine the concentration of binary solutions if the two different components have significantly differing densities. Premixed nitrogen-hydrogen cylinders were tested and the results plotted along with that of pure nitrogen. Fig. 5 shows the density difference between 0, 5.18 and 10.18% hydrogen in nitrogen. Gas concentration resolution not only improves with the increasing difference in the individual gas densities but also with increasing pressure, as shown in Fig. 5. This technology was previously used for liquid binary chemical concentration measurements [12] and, as Fig. 5 shows, can also be applied for binary gas concentration measurements. A variety of gas mixture applications exist including hydrogen fuel cells, welding cover gases, anesthesia, gas-based combustion engines, semiconductor, petrochemical and steel processing.
The new gas density meter has both an on-meter interface (LCD and push buttons) and computer interface. USB and RS-232 digital outputs are available as are 4-20mA analog outputs. The rugged case is IP67 rated to prevent moisture ingress. The unit can operate over a -20°C to 60°C temperature range, a 0 to 20 bar pressure range and go up to gas densities of 30 kg/m3. There is even an option of up to 2 GB of internal data storage for periodic retrieval of sensor data over time. The meter has been employed in slip stream mode on large diameter pipes.
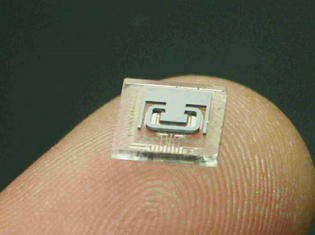
Fig. 6. The MEMS chip and resonating microtube.
Micromachines Sensor Element Fabrication
At the core of the MEMS gas sensor covered in this paper is a resonating silicon microtube, shown in Fig. 6. To begin the tube fabrication process the inner channel is etched into a silicon wafer. Another silicon wafer is fusion bonded onto this. The outer shape of the tube is next defined and this silicon slice is then anodically bonded to a metallized glass wafer. The shape of the resonating tube can be varied by the mask design process, Fig 6 shows a C shaped resonating tube. Plasma etching sets the tube wall thickness, so high pressure, thick walled density sensors can be fabricated with this process. A glass wafer has holes drilled into it that will be the fluid inlet and outlet to the resonating tube. The glass wafer also is etched prior to metal deposition and patterning such that a gap is formed between the silicon tube and the metal capacitive electrodes present on the glass surface after wafer bonding.
A platinum resistive temperature sensor has also been integrated onto the MEMS chip [11]. This element is located just a few microns from the silicon fluid conduit and Fig. 6. The MEMS chip and resonating microtube. Si tube Fig. 7. MEMS integration into the industrial inline density meter. White Paper ‐ A low pressure, light gas concentration and density sensor www.mems-iss.com so gives the chip a very quick temperature response which has been tested up to 150°C [12]. The device can measure the density and temperature. The MEMS chip is wirebonded to the printed circuit board. For industrial applications a robust mechanical housing is used to enclose the MEMS sensor and printed circuit boards (top of Fig. 7) used to for signal processing. The MEMS chip (bottom) is mounted to a stainless steel structure that includes the NPT pipe fittings and internally machined bypass as shown in Fig. 7.
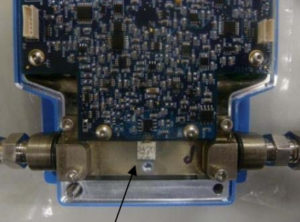
Fig. 7. MEMS integration into the industrial inline density meter.
Conclusions
The measurement of the density and binary concentration of light and heavy gases over a variety of pressures with a micromachined resonant tube sensor in combination with a pressure sensor has been demonstrated. The density sensor incorporates an intrinsically safe design to enable the monitoring of flammable gases such as hydrogen and methane. The density measurement of low pressure (101KPa to 400KPa ) hydrogen gas was demonstrated. Applications for this gas density technology in the energy, semiconductor processing, medical, welding and industrial markets were also discussed.