MassSense® Density Meter: Advancing biofuel measurement to a new level of performance, size and value!
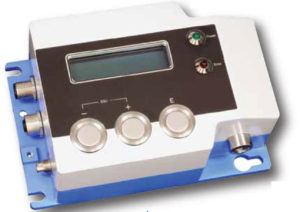
MassSense® Density Meter for biofuel measurement
Accurate measurement of fluid density is important in the manufacturing and utilization of biofuels. The density of a liquid or gas is an indication of the composition of the fuel. Integrated Sensing Systems, Inc. (ISS) has created the MassSense family of density meters that provide a new level of accuracy, performance, speed and value to the biofuels industry. The core technology that makes this possible is a patented* silicon MEMS fluidic density sensor which is at the heart of each MassSense. This silicon sensor can measure both liquid (model MS-LDM) and gas (model MS-GDM) density. Silicon has one third the density of the stainless steel commonly used for constructing traditional density meters, resulting in a sensor with higher density resolution. MassSense has many biofuel applications, which will be highlighted in the following pages.
In ethanol production, MassSense can be used in multiple locations in the plant to improve production efficiency.
Ethanol & Corn
At the exit of the molecular sieve dryers, a MS-LDM will detect water breakthrough, resulting in the most efficient operation of the dryers.
Finally, an ethanol plant wants to produce ethanol that meets the purchasing specification. Water content is part of that specification. MS-LDM can be used to monitor the residual water content in ethanol and control the water content to meet the sales specification.
Fuels
Oil price spikes have accelerated the growth in alternative fuel production. New fuel quality sensing technology is required to measure E85, biodiesel, biojet and even biobutanol fuels. Cost pressures, quality testing and contaminant monitoring drive the need to create sensors that assist in fuel blending, identifying fuel type, and ensuring fuel quality. These alternative fuels have significantly different density and viscosity values compared with traditional fossil fuels. Viscosity can also be used to identify biofuels and the composition of biofuel mixtures. MassSense is designed to be affordable, easy to install and meet stringent electrical safety regulations.
Biodiesel
Density is a very important measurement in the production of biodiesel. MS-LDM is used in biodiesel production to predict numerous fuel parameters such as cetane number and heating value, which depend on density. Density also affects the injection behavior, injection pressure and fuel spray characteristics, which in turn influence engine performance, combustion and exhaust emissions. The fuel injection systems used on diesel engines measure fuel in terms of volume. Consequently any change in fuel density will change the injected fuel mass, resulting in unexpected power output. In biodiesel production, liquid density can be used as an indicator of the quality of produced biofuel. For example, biodiesel that has a high measured density might indicate it contains excess water or glycerol. On the other hand, biodiesel with a low density might indicate excess alcohol in the fuel.
Fuel | Density Range (gm/cc) |
---|---|
Gasoline | 0.725-0.775 |
E85 | 0.775-0.782 |
Ethanol | 0.7856 |
Butanol | 0.8095 |
Fisher Tropsch "diesel" | 0.784-0.801 |
Diesel | 0.822-0.860 |
Biodiesel | 0.860-0.900 |
Butanol E85
E85 is a gasoline and ethanol blend containing 51% to 83% alcohol, depending on geography and season. It is used in flex fuel vehicles. Density can be used at the alcohol/gasoline loading rack to confirm the concentration of ethanol in the fuel. Butanol has a promising future in the biofuel industry as a substitute for ethanol. It has alonger carbon chain and a higher heating value per gallon. MS-LDM can be used to measure butanol concentration in the overhead product of a distillation column and during its production using yeast, algae or bacteria.
Viscosity
MassSense has the additional capability to measure the viscosity of liquid fuels up to 50 cP. The MEMS fluidic sensor detects viscosity as a side effect of making the density measurement. Viscosity can be reported as a trend or as an absolute value. Viscosity is important in biofuel quality measurement because it affects the atomization of the fuel in the injection nozzle. Viscosity can also be used to identify fuel blends.
Gaseous Fuel
The future of green fuels includes gases generated when carbon in biomass is converted, using either bacteria or a thermal process, into gases such as methane and hydrogen, which can then be used as a fuel or chemical feedstock. Gases generated from the anaerobic digestion of organic materials can be captured and used as a fuel. This collection method helps prevent the release of the strong greenhouse gas, methane, into the environment. The MS-GDM gas density meter can be used to check the composition of the gases produced from these processes. The average molecular weight of the gas mixture can be calculated in the MS-GDM using measured gas density, gas absolute pressure and gas temperature. Since hydrogen has a molecular weight of 2, methane 16 and carbon dioxide 44, the average molecular weight of the off-gas from these processes is an indicator of the composition of the gas. Biogas heating value is critical to the efficient operation of the internal combustion engine used to convert biogas into electric power. The MS-GDM can estimate the biogas heating value very quickly and allow the fuel control system to add supplemental natural gas to maintain a minimum heating value The MS-GDM gas density measurement approach is simple, fast and more cost effective than the use of optical analyzers, gas chromatographs or calorimeters. Integrated with every MS-GDM is an absolute pressure sensor, which is used to generate accurate gas density measurement with fluctuating gas pressure.
Biomass Gasification
An alternative methodology for converting biomass into fuel is to use a high temperature gasification process to convert carbon into hydrogen and carbon monoxide. This syngas is further processed to create liquid fuels and green chemicals. The MS-GDM is the perfect meter for detecting the purity and molecular weight ratios of the gases produced from this gasification process.