This article presents a MEMS chemical sensor, shown in Fig. 1, which has been under developed specifically for the fuel cell chemical concentration market for over three years. This microfluidic technology has previously been used to measure fluid density, chemical concentration in a laboratory setting [1] and mass flow rate [2]. It uses a getter assisted, vacuum packaged [3], single crystal silicon resonating tube along with an integrated thin film RTD.
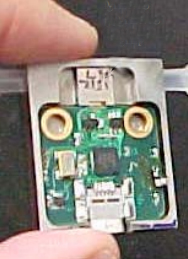
Fig. 1. MEMS-based methanol concentration sensor.
Direct fuel cells do not reform the fuel into hydrogen gas but directly produce electricity using air and fuels such as aqueous solutions of methanol, ethanol or formic acid. One problem that has hampered the use of these fuel cells is membrane crossover. Membrane crossover occurs when the fuel to water concentration gets too high and fuel goes through the membrane to the other side of the fuel cell. A high fuel concentration lowers performance due to crossover and membrane damage while a high water concentration starves the system of fuel, again lowering performance [3]. A fuel to water concentration sensor is often employed in active direct fuel cells to optimize fuel cell performance, but a robust sensor has not been developed. Direct Methanol Fuel Cells (DMFCs) are the most common direct fuel cells and are being actively developed for laptop computers, digital cameras, battery recharging stations and digital assistants with initial product launches anticipated in 2008. Methanol is relatively inexpensive, easy to handle transport and store. It is critical from an economic standpoint that the sensor work over a wide temperature range, be relatively small so that it can be embedded in a portable system and is capable of being manufactured at a low cost.
Experimental
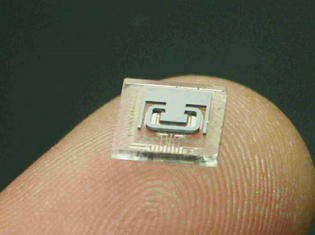
Fig. 2. A decapped, MEMS chip, on a finger tip, showing the microtube and metal pattern.
The frequency of the microtube and a thin film resistor are used to provide a fluid density and temperature output, which are employed to produce a chemical or methanol concentration. Fig. 2 shows the resonant microtube. This tube is driven electrostatically while the tube’s vibration frequency is sensed capacitively.
In this photograph the silicon cap which seals the resonator in vacuum has been removed. This silicon cap contains a getter to reduce the cavity pressure. The cap is sealed to the glass wafer via wafer-to-wafer bonding. Fluid is admitted to the microtube through holes in the back of the metalized glass chip [1-3]. Fig. 3 shows how the methanol to water concentration varies with both density and temperature. A comparison with alternate methanol concentration sensing technologies like ultrasonic and refractive index measurements is made in Fig. 4. The refractive index varies very little as a function of methanol concentration.
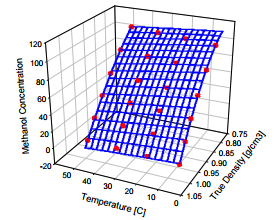
Fig. 3. Methanol to water concentration as a function of density and temperature.
An ultrasonic, speed-of-sound sensor does have a higher sensitivity to methanol concentration changes at concentrations above 40% than density, but has a flat portion in the sensitivity curve and then a reversal in slope at lower methanol concentration values, where DMFCs operate. Density measurement appears to be the best available means of sensing methanol concentration for DMFCs. Methanol concentration was measured using the MEMS device over the typical consumer electronics temperature range of use, 10°C to 50°C. Different methanol to water concentrations were prepared ranging in concentrations from 0.6 Moles/liter up to 3 Moles/liter and is shown in Fig. 5.
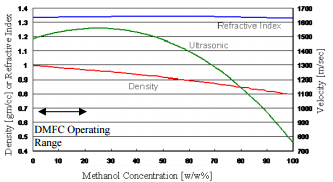
Fig. 4. Concentration plots using three methods of measuring methanol concentration – speed of sound, refractive index and density.
For other applications such as testing petrochemicals, this MEMS resonating sensor has been operated at 150˚C. To accommodate higher flow rates a compact, by-pass package design has been developed, with a transition to low-cost plastic electro-fluidic packages as the final goal. The novel by-pass package design opens this technology up to many high-flow rate applications [5].
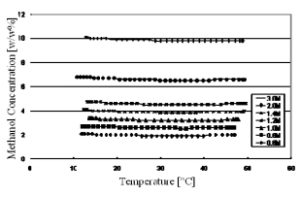
Fig. 5. Methanol concentration test output of the sensor over temperature and concentration.
A benefit of using the mass-based density sensor technology over an electrochemical method is the virtual immunity of the technique to low concentrations of DMFC reaction byproducts. In addition to low speed, electrochemical methanol concentration sensors will have problems with chemical impurities. The MEMS-chip based density sensor has been used to test the concentration of sulfuric acid solutions, solvents and petrochemicals with no change in sensor performance [1]. Formic acid is a common DMFC by-product.
Typical DMFC systems will have formic acid concentrations of up to 100 ppm. Very little impact on formic acid concentration was noted between 50 ppm and 100 ppm. At 1000 ppm the relatively dense (1.222 gm/cc for formic acid versus 0.791 gm/cc for methanol at 20°C). impurity began to introduce a slight error in the mass-based measurement method. Fig. 6 shows another plot of seven methanol concentrations, each with an additional 1000 ppm of formic acid added to the solution.
Again, the sensor output over temperature is consistent at all concentration levels between 0.6 Moles/liter and 3 Moles/liter with the addition of the formic acid impurity. Since this sensor is mass-based it can be applied to other fuel cells types and fuels, including active ethanol, ethylene glycol and formic acid [6] direct fuel cells. The technology is also being applied the ethanol and butanol quality monitoring as well as biodiesel fuel blending [7,8]. Water absorption is a problem for ethanol distillation and density measurement is an excellent method of checking for water contamination. Table 1 shows how density can be monitor the type of fuel employed. E85 is an 85% ethanol-15% gasoline fuel. The fuel type can clearly be distinguished using a density measurement.
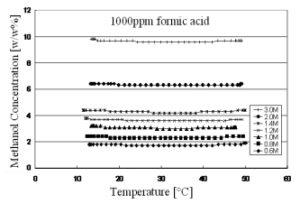
Fig. 6. Methanol concentration plot over temperature with 1000ppm of formic acid present.
Fuel | Density Range (gm/cc) |
---|---|
Gasoline | 0.725-0.775 |
E85 | 0.775-0.782 |
Diesel | 0.822-0.860 |
Biodiesel | 0.860-0.900 |
Conclusions
A mass-based methanol concentration sensor for controlling the methanol to water concentration in a DMFC system was described. The sensor is based on a microfluidic chip that employs a resonant microtube and on-chip platinum temperature sensor to measure the density of a fluid. Using the density and temperature output the MEMS methanol concentration is determined. The sensor was found to have a linear output between temperatures of 10°C to 50°C at methanol concentrations of between 0.6M and 3M. In tests with petrochemicals the sensor operated at 150°C. Formic acid contaminants under concentrations of 100 ppm did not affect the accuracy output of the methanol sensor.
The mass-based density sensor was found to perform better over temperature than methanol sensors based on refractive index or ultrasonic speed of sound measurements. The density sensing approach meets the performance requirements with respect to methanol concentration, temperature and resistance to chemical impurities required for an embedded DMFC application. A MEMS-based density sensor also has application to petrochemicals and biofuels including ethanol, butanol and biodiesel.