Abstract
A MEMS-based chemical concentration sensor for monitoring and controlling the methanol to water ratio in a Direct Methanol Fuel Cell (DMFC) is described. This sensor is based on a vacuum packaged resonant microtube and on-chip platinum temperature sensor to measure the density of a fluid. Using the density and temperature output the methanol concentration is determined. The performance of the sensor over temperature, concentration and in the presence of formic acid by-products is examined. Additional test results and applications for other fuels and biofuels are presented including ethanol, ethylene glycol, butanol, gasoline and diesel fuel.
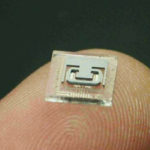
Fig 1. A decapped, MEMS chip, on a finger tip, showing the microtube and metal pattern.
Introduction
Methanol is the fuel used in Direct Methanol Fuel Cells (DMFCs) and reformed fuel cells. As a fuel, methanol is relatively inexpensive, has a high specific energy density, is easy to handle transport and store. Commercializing this fuel cell technology has run into performance and efficiency problems with methanol crossover [1-5). Methanol crossover is a term used to describe methanol transport through the fuel cell membrane without reaction or generating electric current. Methanol crossover lowers fuel cell efficiency and can chemically damage the membrane. DMFC performance can be impacted by the methanol to water concentration [1-5], temperature [2,3,6,7], flow rates [7] and the system membrane [3-7). In active DMFC systems a control loop employing a methanol concentration sensor to optimize the methanol to water concentration can boost DMFC performance. Any sensor used in commercial applications must be able to perform over a wide range of methanol concentrations and temperature and in the presence of chemical impurities. It is critical from an economic standpoint that the methanol sensor is small so that it can be embedded in a portable system and capable of being manufactured at a low cost. This paper presents a MicroElectroMechanical Systems (MEMS) sensing chip that is being developed for the methanol concentration application. This device has previously been used to measure fluid density and chemical concentration [8,9). As the mass of the total tube/liquid system increases the vibrational frequency decreases. This basic operational principle is used to determine the concentration of methanol in the aqueous solution. The higher the methanol concentration is, the higher the resonant frequency output. Other MEMS devices have been adapted to severe, high-volume, relatively low cost applications in the automotive and medical industries (10) so it is anticipated that this technology could provide both a technical and commercial solution for embedded methanol sensing in active DMFC powered systems.
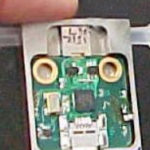
Fig 2. MEMS-based methanol concentration sensor.
In addition to methanol-water fuel cells, other fuels and biofuels can benefit from a small concentration, high-resolution density meter or quality sensor. Ethanol, methanol and butanol have been used as a biofuel additive to gasoline for intemal combustion engines (11,12). Water is fully soluble in ethanol, and as a result water contamination and associated fuel tank and fuel line corrosion has emerged as a problem with ethanol-gasoline fuels:Because of the corrosive problems associated with ethanol, it cannot be transported via a pipeline and must rely on tanker delivery. Water is only partially miscible in butanol and as a result could be superior to ethanol as an alternative biofuel additive [ 12J. A density measurement is an excellent method for determining the water levels in both ethanol and butanol and data will be presented in this paper. The use of a liquid density measureless to distinguish between different biofuels, petrochemical fuels and standard mixtures will be demonstrated.
Experimental
The resonant microtubes used in this paper employ a MEMS fabrication process, which uses a combination of plasma and wet etching, photolithography, along with wafer bonding to form the microfluidic chips [8,9). Fig. l shows an uncapped microtube resonatonhip. The silicon tube, shown in Fig. 1, is anodically bonded to glass. This glass wafer has the metal electrodes and runners used to carry electrical signals. A thin-film metal layer is used as an on-chip, resistive temperature sensor. The resonator is finally vacuum packaged at the wafer level using a thin film getter [ I 3] to reduce the external damping of the vibrating microtube. Two holes in the bottom of the glass chip admit fluid into the silicon microtubes.
The MEMS chip requires external electronics to amplify the signal and drive the microtube into resonance: in addition, the signal is processed to obtain a methanol concentration value. The tube is driven into resonance electrostatically and its motion sensed capacitively using metal electrodes under the tube and accompanying electronic circuits connected to the MEMS chip via wire bonding. All sensor operation voltages are below 5 V.
Fig. 2 shows the packaged sensor with the microchip and its fluidic and electrical interface and associated electronics on a single printed circuit board. The tubing on the sensor is connected into the fluid path of the DMFC. This system operates at a flow rate of 25 mL/min, which is common for consumer electronic DMFC systems. These relatively high flow rates cannot be accommodated using a standalone microtube due to highpressure drop. To enable the use of higher flow rates a bypass package design is employed [14]. The system is designed to operate between 5 and 50 °C. The device shown in Fig. 2 is a third generation methanol concentration sensor prototype, designed to fit into small portable DMFC systems.
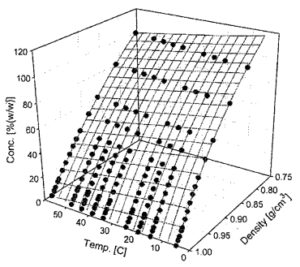
Fig 3. A methanol-water concentration, density and temperature plot.
Results and Discussion
Fig. 3 shows that a predictable slope in the density value was observed with changing methanol to water concentrations. However, the density of any fluid varies with temperature. As such, the characterization and mapping of methanol to water concentration over temperature is key to arriving at an accurate methanol concentration value. Fig. 3 shows a three-dimensional plot of how both densities vary as a function of methanol concentration and temperature. Data points were used to build a three-dimensional surface of this relationship. This relationship must be stored in the sensor’s electronic memory to enable an accurate measurement of concentration.
A basic methanol concentration sensor was calibrated using the data in Fig. 3. Next methanol concentration was measured over the typical consumer electronics temperature range of use, 10-50 °C. Seven different methanol to water concentrations were prepared ranging in concentrations from 0.6 up to 3 moles/L. This covers the common methanol concentrations employed to minimize crossover efficiency losses [1-5]. The experimental values obtained are plotted in Fig. 4. The sensor output for the fixed concentrations are flat with respect to temperature. It should be noted that the resonant sensor works over the full 0-100% methanol concentration as shown in Figs. 3 and 4.
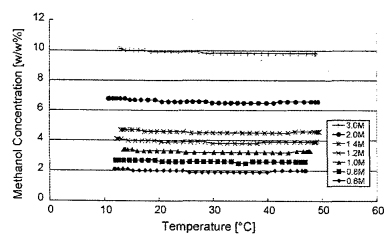
Fig. 4 Methanol concentration (%) sensor output as a function of temperature for different solution formulations (M).
A benefit of using the mass-based density sensor technology over an electrochemical method is the virtual immunity of the technique to low concentrations of DMFC reaction byproducts. The MEMS-chip-based density sensor has been used to measure the concentration of sulfuric acid solutions, solvents and petrochemicals with no change in sensor performance (8). Formic acid is a common DMFC by-product. The following table shows how the sensor output varied with different concentrations of formic acid. Typical DMFC systems will have formic acid concentrations of up to 100 ppm. Table I shows that very little impact on formic acid concentration was noted between 50 and 100 ppm. As would be expected, at 1000 ppm the relatively dense (l .222 g/cm3 for formic acid versus 0.791 g/cm3 for methanol at 20 °C) impurity began to introduce an error in the mass-based measurement method. Fig. 5 shows another.· plot of seven methanol concentrations, each with an additional 1000 ppm of formic acid added to the solution. Again the sensor output over temperature is consistent at all concentration levels between 0.6 and 3 moles/L with the addition of the formic acid impurity.
To summarize the discussion on methanol fuel cell sensing, a fluid density measurement technique can be employed to produce a robust methanol concentration sensor. This approach has been found to work over concentrations and temperatures of interest for active DMFC systems. As has been mentioned the MEMS-based density sensor chip contains a resistive temperature sensor that in addition to assisting in increasing the density measurement accuracy and response speed could be employed in a DMFC system to monitor the fluid and system temperature, which is critical in maintaining optimum performance [2,3,6,7]. The prototype system shown in Fig. 2 has an accuracy of under ±0.3% concentration with a 1-3 s response time for a flow rate of 25 mUmin and operates between 5 and 50 °C.
MMC* | 0 ppm FA | 50 ppm FA | 100 ppm FA | 1000 ppm FA |
---|---|---|---|---|
0.6 | 2 | 2 | 2 | 1.8 |
0.8 | 2.7 | 2.7 | 2.7 | 2.3 |
1.0 | 3.4 | 3.3 | 3.3 | 3.1 |
1.2 | 4.1 | 4 | 4 | 3.7 |
1.4 | 4.7 | 4.7 | 4.7 | 4.3 |
2.0 | 6.8 | 6.7 | 6.7 | 6.3 |
3.0 | 10.2 | 10.1 | 10.1 | 9.7 |
Since this sensor is mass-based it can be applied to other fuel cell fuels including ethanol and ethylene glycol, as illustrated in Figs. 6 and 7. The technology can also be applied to ethanol and butanol quality monitoring as well as biodiesel fuel blending [15,16]. As was mentioned in Section I, water absorption is a problem for ethanol distillation and a density measurement is an excellent method of checking for water contamination. Large capacity for corn-based ethanol manufacturing already exists and is growing ( 4.4 billion gallons/year US capacity in 2004) and the capacity to· produce methanol is growing as well (1.2 billion gallons/year US capacity). There are already 585 ethanol (E85) stations in the US with the number growing to 2500 by the end of 2007 for internal combustion engine applications. E85 is an 85% ethanol-15% gasoline fuel. GM and Ford have already made millions of vehicles that are E85 compatible (17). The short-term adoption of E85 fuels could be a stepping-stone to ethanol or methanol-based reformed fuel cells for transportation. Because of differing refining and fuel blending processes, the density of commercial fuels will vary within a range. Table 2 shows the published biodiesel (15,16] and measured gasoline, E85 and diesel fuel density ranges. A density measurement is able to distinguish the type of fuel with a high degree of accuracy.
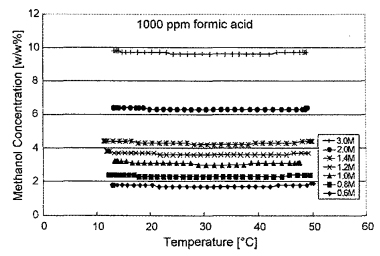
Fig 5. Methanol concentration as a function of temperature with a formic acid impurity concentration of 1000 ppm.
Unlike ethanol, water is only partially miscible in butanol and as a result is an alternative biofuel additive to ethanol with less corrosive issues and can be transported more economically via pipelines and make a better biofuel additive for gasoline. Table 3 shows that a density measurement is an excellent method for determining the water levels (in weight percent) in butanol. This type of sensor may find an application as a butanol quality meter.
Integrating these sensors onto a vehicle is a potential future application. Key to operation in the automotive environment is the ability of the technology to withstand a wider temperature range than what is required on fuel cells used in consumer electronics. Operating temperatures go as high as 125 °C in the engine compartment and as high as 150 °C when mounted on an internal combustion engine (10]. Fig. 8 shows how the resonant frequency of an air filled microtube varied between 60 and 150 °C. This change is primarily due to the change in Young’s modulus of silicon. The upper limit on functionality was found to be the electronics, not the MEMS resonator. The resonance frequency of these tubes are above 10 kHz, which reduces the susceptibility of the sensor to common vibrational frequencies experienced in the automotive environment ( <2 kHz).
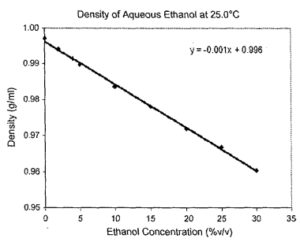
Fig 6. The density plot for ethanol-water at 25 degrees Celsius.
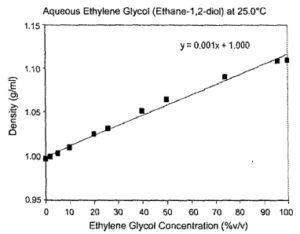
Fig. 7 The density plot for ethylene glycol-water at 25 degrees Celsius.
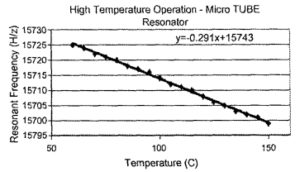
Fig 8. High temperature test data for microtube resonator. A frequency vs. temperature plot.
Fuel | Density Range (g/cm3) |
---|---|
Gasoline | 0.725-0.775 |
E85 | 0.775-0.782 |
Diesel | 0.822-0.860 |
Biodiesel | 0.860-0.900 |
Percent (1-butanol) in H2) (w/o) | Density (g/cm3) |
---|---|
88 | 0.83361 |
90 | 0.82823 |
92 | 0.82552 |
94 | 0.82144 |
96 | 0.81794 |
98 | 0.81374 |
100 | 0.80951 |
Conclusions
A mass-based methanol concentration sensor for controlling the methanol to water concentration in a DMFC system was described. The sensor is based on a microfluidic chip that employs a resonant microtube and on-chip platinum temperature sensor to measure the density of a fluid. Using the density and temperature output the methanol concentration is determined. The sensor was found to have a linear output between temperatures of 10 and 50 °C at methanol concentrations of between 0.6 and 3M. Formic acid contaminants under concentrations of 100 ppm did not affect the accuracy output of the methanol sensor. The density sensing approach appears to meet the performance requirements with respect to methanol concentration, temperature and resistance to chemical impurities required for an embedded DMFC application. The MEMS sensor was also shown to perform well as a concentration and quality sensor for aqueous solutions of ethanol, butanol and ethylene glycol. The sensor was able to distinguish between gasoline, E85, diesel and biodiesel fuels. Operation at temperatures as high as 150 °C was shown, which opens up the sensor to automotive applications.