Abstract
Density measurements have long been used to monitor petrochemical distillation. The density of the petrochemicals decreases as one moves up the distillation column. Measuring the density or specific gravity of biodiesel has been reported to be the preferred method of blending biodiesel fuel for both accuracy and ease of use. To see widespread use, a measurement technology must not only be capable of accurately monitoring a parameter, but it must do so in an economical way. This paper explores the application of microelectromechanical systems technology to fuel monitoring, quality control, and blending.
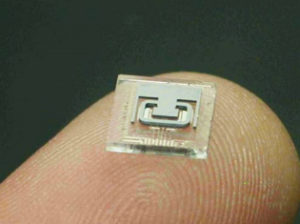
Fig. 1 – A decapped MEMS chip, on a finger tip, showing the microtube and metal pattern.
This microfluidic sensor has on-chip density/specific gravity, temperature, and viscosity measurement capabilities, as will be demonstrated in the experimental results. The ability to differentiate between gasoline, ethanol, diesel, biodiesel, butanol, Fischer–Tropsch fuel, water, and air contamination with a density measurement and in some cases a viscosity measurement will be demonstrated. Using gravimetric measurements, based on fluid density, concentrations of fuel blends like ethanol-gasoline can be measured. Contamination levels of water in ethanol can also be measured in this manner. The density of fuel over temperature can be made with this sensing technology and applied to custody transfer. Potential microfluidic clogging issues are addressed by filtration and by adding the capability of sensing flow through the sensor. Measuring fluids under high flow rates is accommodated with a bypass design. An intrinsically safe circuit has been developed to enable use of this technology with flammable liquids. Vibration testing has been undertaken to show that these micromachined devices, with their high resonant frequencies, are immune to vehicular and aviation vibration, unlike conventional density meters made using larger resonating steel tubing.
![Fig. 2—The ISS FC-10 density and methanol concentration sensor [10].](https://metersolution.com/wp-content/uploads/2016/09/Monitoring-and-Blending-Biofuels-Using-a-Microfluidic-Sensor-2-300x227.jpg)
Fig. 2—The ISS FC-10 density and methanol concentration sensor [10].
Density measurement has commonly been employed to monitor petrochemicals in refineries. The density of the petrochemicals decreases as one moves up the distillation column. Table 1 shows the published biodiesel [1–3] and measured gasoline, E85, and diesel fuel density ranges. Because of differing refining and fuel blending processes, the density of commercial fuels will vary within a range. Table 1 shows that a density measurement is able to distinguish the type of fuel with a high degree of accuracy. Table 1 also shows that density can also be used to detect water and air bubbles in fuel or lubricants. Water contamination can be a problem with pipe transport and tank storage. Trapped water at the bottom of a fuel tank can be detected easily via density.
Measuring the density or specific gravity of biodiesel has been reported to be the preferred method of blending biodiesel fuel for both accuracy and ease of use [1]. Ethanol is the most established biofuel market, with an early start in Brazil [4] and a more recent expansion into the United States [5,6]. While ethanol can reduce imported oil, it does have disadvantages in lower gas mileage and contribution to the corrosion of the fuel system. To improve gas mileage and remove water, ethanol is generally blended with gasoline. Ten (E10) and eighty five percent (E85) ethanols are the most common blends, although E20, E30, and E40 are also in use. Two tank systems, one with ethanol and one with gasoline, can be used to generate a wide variety of fuel blends.
Fuel/Fluid | Density Range (gm/cm³) |
---|---|
Air | 0.001 22 |
Gasoline | 0.725–0.775 |
E85 | 0.775–0.782 |
Ethanol | 0.7856 |
Butanol | 0.8095 |
FT "diesel" | 0.784–0.801 |
Diesel | 0.822–0.860 |
Biodiesel | 0.860–0.900 |
Water | 0.999 04 |
Another potential long term solution to the U.S. dependence on Middle Eastern oil imports is the development of Fisher–Tropsch (FT) fuels. These liquid fuels are produced from hydrocarbon feedstock like coal, natural gas, or oil shale. The U.S. military has taken the lead in this area with a long term goal on replacing 75% of the oil imports by 2025 [7,8]. These reserves offer the equivalent oil reserve of 2.3 trillion barrels, more than three times the Middle East oil reserves. The main measurable difference between FT fuel and petrochemical fuel is density.
To a widely adopted measurement technology, the method must not only be capable of accurately monitoring a parameter, but it must do so in an economical manner. This paper explores the application of microelectromechanical systems (MEMS) technology to fuel monitoring, quality control, and blending. This new sensor has already been developed for the laboratory, industrial density, and specific gravity measurements and fuel cell concentration sensing applications [9–11]. Other MEMS devices have been adapted to severe, high-volume, and relatively low cost applications in the automotive [12], consumer, and medical markets, so there is confidence that this technology will provide both technical and commercial solutions for fuel quality, custody transfer, and blending sensing applications.
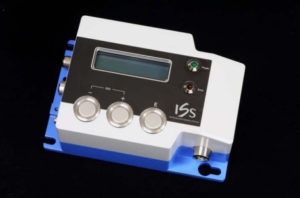
Fig. 3 – The intrinsically safe FuelSense, MassSense, density meter.
Experimental
The resonant microtubes used in this paper employs a MEMS fabrication process, which uses a combination of plasma and wet etching, photolithography, and wafer bonding to form their microfluidic chips [9]. Figure 1 shows an uncapped microtube resonator chip on a finger tip. The hollow silicon tube, shown in Fig. 1, is anodically bonded to glass. This glass wafer has the metal electrodes and runners used to carry electrical signals. The thin-film metal layer is also used as an on-chip, resistive temperature sensor. The resonator is finally vacuum packaged at the wafer level to reduce the external damping of the vibrating microtube. Two holes in the bottom glass chip admit fluid into and out of the silicon microtube.
The MEMS chip requires external electronics to amplify the signal and drive the microtube into resonance; in addition, the signal is processed to obtain a density value. The tube is driven into resonance electrostatically and its motion sensed capacitively using metal electrodes under the tube and accompanying electronic circuits connected to the MEMS chip via wire bonding. All sensor operation voltages are below 5V. As the mass of the total tube/liquid system increases, the vibrational frequency decreases.
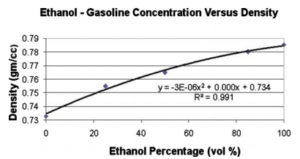
Fig 4. – The density plot for ethanol-gasoline at 25 degrees Celsius.
This technology and the model FC10 family of in-line density meters and fuel cell sensors, shown in Fig. 2, was first applied to measuring methanol-water concentration in a direct methanol fuel cell DMFC system [10] as well as the density of nonflammable fluids. Without an accurate feedback of methanol to water concentration sensor, active DMFCs cannot perform efficiently.
The sensing concept is universal for virtually any fluid or liquid solution. The density of the fluid liquid or gas can be measured using the vibrational frequency of the microtube. For binary solutions, this has been used with methanol and ethanol fuel cells to measure concentration. Petrochemicals and biofuels can use the density or American Petrochemical Institute output to indicate the type of fuel and its purity and to blend fuels together. Figure 3 shows an intrinsically safe density sensor designed by Integrated Sensing Systems (ISS). This device can be used with all types of liquid and gas fuels and fuel blends. High flow rates cannot be accommodated using a microtube due to high pressure drop. To enable the use of higher flow rates, a bypass package design is employed [11]. By using the Coriolis mass flow effect associates with resonating tubes [13], the presence of fluid flow during the density measurement versus a stagnant condition associated with a clogged line can be detected with this device.
1-Butanol in Water (wt%) | Density (gm/cm³) |
---|---|
88 | 0.833 61 |
90 | 0.828 23 |
92 | 0.825 52 |
94 | 0.821 44 |
96 | 0.817 94 |
98 | 0.813 74 |
100 | 0.809 51 |
For fluid testing, NIST certified density/viscosity calibration standards labeled N2 and N4, purchased from Cannon Instruments Co., were used in this investigation. These standards covered the range of typical fuels. In addition, other fuels and liquids such as dextrose sugar solutions in water, isopropyl alcohol, methanol, and degassed and deionized water, were first tested in a Brookfield DV-I viscometer and Anton Paar 4500 density meter, and/or the density and viscosity values were obtained from the literature 14 for pure fluids. The fluids were then tested using the micromachined sensors described in this paper. The density and viscosity values obtained with the sensor described in this paper were compared to the calibration standards and to data taken from these other laboratory instruments. The majority of the tests were done at room temperature, but testing between 17 to 52°C was undertaken and was cooled or heated using an attached Peltier panel. Temperature was also used to change the viscosity of test fluids. The chemical mixtures were made volumetrically for the density versus concentration plots and tables. The density versus concentration and temperature data were plotted using Excel.
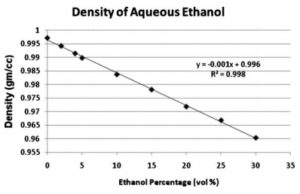
Fig 5. – The density of ethanol-water solutions at room temperature.
Results and Discussion
Density measurements were made to demonstrate the ability of using this parameter to both distinguish between different fuels and detect contaminants like water and to blend miscible fuels together. Table 1 showed literature data for the densities of different fuel types. Ethanol-gasoline blending is perhaps the most common biofuel-petrochemical mixture in use worldwide. Figure 4 shows how the density of this blended fuel varies at room temperature. One drawback of ethanol is its water solubility and the resulting corrosion of pipes, tanks, and tubing using ethanol and ethanol-gasoline mixtures. Special materials like stainless steel are often required for reliable handing of ethanol blends. Because of this water-related corrosion issue, ethanol must be transported by tanker truck only and not pipelines. Density can be used to monitor the water content of ethanol as shown in Fig. 5. This method can be used at distilleries and storage tanks to detect water contamination of alcohols.
Unlike ethanol, water is only partially miscible in butanol [15] and as a result is an alternative biofuel additive to ethanol with less pipeline corrosion. This enables butanol to be transported more economically via pipelines and make it a potentially better biofuel additive for gasoline than ethanol. Table 2 shows that a density measurement is an excellent method for determining the water levels in butanol. This type of sensor may find an application as a butanol quality metre. Density technology can be applied to ethanol and butanol quality monitoring as well as biodiesel fuel blending [2,3,15–19].

Fig 6. – The density of diesel fuel versus temperature.
The density of any fluid varies with temperature. Figure 6 shows how the density of diesel fuel varies over temperature. Similar relationships exist for different fuels. This variation in fuel density and hence delivered mass in the aviation market is an application for this technology with respect to fuel custody transfer. Aviation fuel is sold volumetrically but employed in aircraft by mass, which can, over a wide fuel delivery temperature range of use, result in cost variation for the end user. The micromachined resonating tubes have been operated at temperatures as high as 150°C [10].
In addition to density, this technology can measure viscosity [20], which may be useful for biodiesel. The resonator output for several fluids was used to develop a dynamic viscosity output for the sensor shown in Fig. 7. Fig. 7. Table 3 lists some of the experimental data taken for density and viscosity along with reference data for fluids in the viscosity range of typical fuels. The kinematic viscosity values listed in Table 3 are obtained by using the sensor density and dynamic viscosity data and Eq 1. The kinematic viscosity cSt or mm2 /s of a fluid is given by the expression
v= n/p [1]
where:
n = dynamic viscosity
p = density gm/cm3 of the fluid
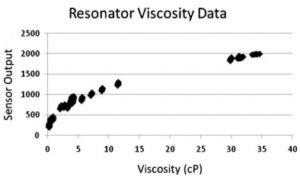
Fig 7. – The amplified resonator output at room temperature as a function of viscosity for a variety of fluids.
The samples sizes for the Table 3 data ranged from 92 to 804 readings per liquid. The standard deviations for density ranged from 0.000 03 to 0.000 11 g/cm3 and for viscosities from 0.014 to 0.025 cP for both the experimental data and reference data over the temperature variation of the tests. Good agreement is found between the measurements and the reference data for the density and dynamic viscosity. The error from the references in ranges from 0.006 to 0.15 cP, or 0.6–8 %.
The viscosity range of gasoline is 0.46–0.88 cSt, of petrochemical diesel 2D is 1.9–4.1, and of biodiesel is 1.9–6.5 or 3.5 to 5.0 depending on the standard [3,18,19]. Table 3 and Fig. 7 shows that the microtube can be used to measure viscosities in this range and may improve the monitoring capability of a density reading with no additional instrumentation. Table 3 shows that water slugs in fuel lines or separated water in tank storage can be distinguished from fuels with density, while alcohols, with a lower overlapping density, could employ a viscosity reading to discriminate them from petrochemical fuels.
Liquid | T ( °&8451;) | ρ (gm/cm³) | ρref (gm/cm³) | N (cP) | Nref (cP) | v (cSt) |
---|---|---|---|---|---|---|
N4 | 28.4–28.7 | 0.7854 | 0.7855 | 4.03 | 4.15 | 5.13 |
N2 | 29.4–29.7 | 0.7837 | 0.7844 | 1.747 | 1.898 | 2.23 |
Water | 25.4–25.5 | 0.9969 | 0.9969 | 0.866 | 0.861 | 0.868 |
Methanol | 25.6–25.7 | 0.7871 | 0.7871 | 0.542 | 0.57 | 0.688 |
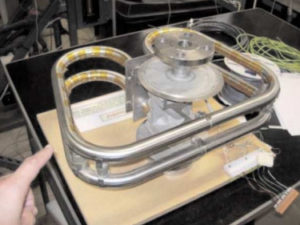
Fig 8. – Example of stainless steel tube Coriolis mass flow / density meters.
Conventional resonating tube density sensors and Coriolis mass flow meters are made of glass and metals like stainless steel [21,22], as shown in Fig. 8. Price, size, and weight are the main force preventing these devices from wider use. A MEMS chip-based sensor has a significant cost and size advantage over the larger, hand assembled steel tube flow and density sensors. The same tubes used to take the density values in this paper have also been used to measure mass flow rate [13]. This capability gives this density measurement technology the ability to monitor for line clogging via this flow data. This capability is beneficial for bypass systems as well to ensure that fuel is flowing through the sensor.
Since all Coriolis mass flow and density meters are vibratory devices, vibration sensitivity has been an underlying problem with this technology. This is a critical problem for industrial, automotive, and aerospace applications where shock and vibration are commonplace. Conventional metal tube density meters resonate at 100–1500 Hz [21,22], leaving them susceptible to the spectrum of common external mechanical vibration and shock frequencies, which are under 2000 Hz.
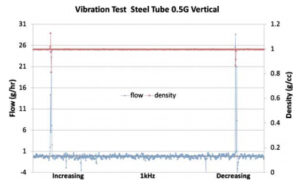
Fig 9. – Density and flow errors in stainless steel tube Corilis meters under vibration.
To examine the difference between the MEMS sensor in this study and a conventional steel tube device, both were placed on a vibratory test stand and cycled from 10 to 1000 Hz starting at 0.5 g and going to 2 g acceleration while monitoring the zero flow rate output of a water filled tube. Figure 9 shows that the conventional steel Coriolis meter had both large flow and density output spikes at its resonance frequency at very low accelerations, 0.5 g. The silicon tube used in the MEMS sensor in this study has resonant frequencies ranging from 20 to 30 KHz, well above what is typically experienced in an industrial, automotive, or aerospace application. The zero flow rate output of the MEMS tube was within a +/- 1 gm/h band at all external vibrational frequencies at 2 g, as shown in Fig. 10. The density output of the MEMS sensor was not affected by vibration. This is an advantage for the MEMS-based Coriolis mass flow and density meters over conventional steel tube technology and can broaden the field of use to include applications with significant vibration and shock, like the trucking and aerospace markets.
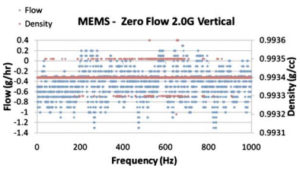
Fig. 10 – Density and flow error versus vibrational frequency at 2 g for water for the MEMS-based sensor.
Conclusions
It was shown that petrochemicals-based fuels and biofuels can be monitored for concentration, purity, water content, and grade using density and viscosity. The technology can also measure temperature and whether fuel is actually flowing through the sensor. Operating on the same principle as conventional steel Coriolis meters, the sensing element is small enough to fit on your finger tip. This size advantage and its associated cost savings enable this sensing capability to be distributed across new areas in fuel and chemical management.