Extending the Lower End of Density Flow & Flowrate Measurement
Coriolis mass flowmeters and resonant densitometers have been used in a high flowrate industrial fluid monitoring applications for decades. These meters utilize a resonating tube, usually made of stainless steel or other corrosion resistant metals or alloys, or in some cases glass. Stainless steel Coriolis mass flowmeters with 12-inch diameter tubes, several meters long and handling flowrates up to 40,000kg/hr, are in common use today.
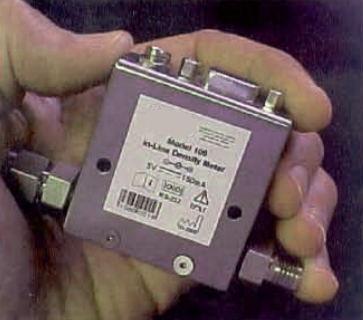
Figure 1. A MEMS-based chemical concentration / density sensor.
At the other end of the fluid metering spectrum, MEMS (MicroElectroMechanical System) technology is being used to make extremely small, fast, and accurate density and flowrate measurements via the Coriolis method. One such MEMS-based flowmeter is shown in Figure 1.
MEMS Coriolis Applications
The fluid density measurement methodology for MEMS-based Coriolis flowmeters is simple -the heavier or more dense the fluid, the lower the resonant frequency of the filled tube. This can be used to obtain a simple density or specific gravity measurement or In a binary solution to monitor chemical concentration.
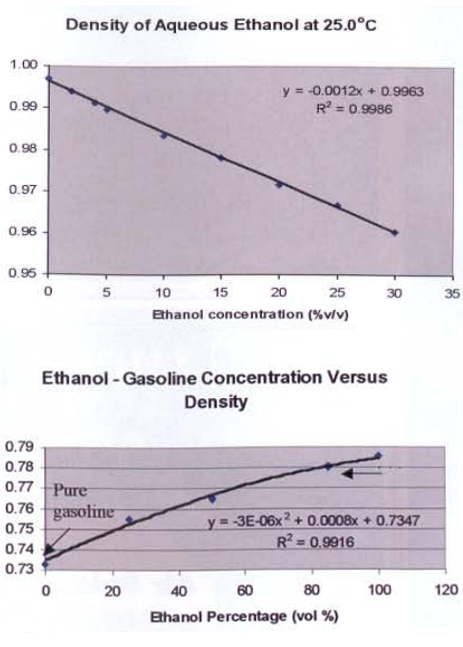
Figure 2. – Chemical concentration plots based on density.
Some of the emerging applications for chemical concentration include alcohol-to-water concentrations in fuel cells and ethanol-to-gasoline concentrations in
ethanol-blended fuels in automobiles. Figure 2 shows concentration-versus-density plots for two such examples.
Small MEMS-based sensors are ideal for portable applications like fuel cell powered laptop computers, where an optimized water-to-methanol concentration is needed to reduce membrane crossover and optimize the efficiency of the fuel cell. For ethanol-blended fuels, the sensor lets the engine control module know the gasoline-to-ethanol ratio to maintain optimum operating conditions. Other applications for density sensors exist in the pharmaceutical, biomedical, nuclear, perfume, petroleum, and beverage industries, as well as in distilleries, hematology, and urology. The device can also be used to measure proof, Brix, Plato, and API gravity. The beverage industry uses densitometers for determining sucrose, alcohol, and extract percentages. Since distilleries are taxed based on alcohol content, measurement accuracy is of great importance.
Small Size, Big Performance
Microfluidics can be limited in many real-world situations by the amount of fluid that can pass through a tiny chip. Obviously, if all fluid must go through a tube the diameter of a human hair, the maximum flowrate of the measuring device is limited. To overcome this problem in the field of density and chemical concentration measurements, some MEMS-based meters employ a bypass design. Figure 1 shows a MEMS-based industrial densitometer that can utilize %” tubing. This enables relatively high flowrate density-and chemical-concentration measurements with the size andcost saving benefits of microchip technology.
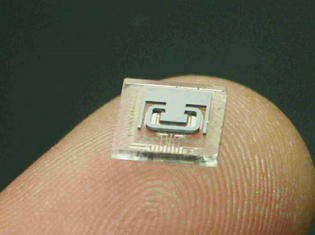
Figure 3. – MEMS sensor chip.
The micromachine shown in Figure 3 is made up of a silicon microtube that resonates over a set of metal capacitor plates. The resonant tubes are on the micro-to-millimeter scale and can easily fit on the tip of a finger. These small metal plates and traces are patterned on a glass chip. One metal plate electrostatically drives the tube into resonance, while another measures how the tube is vibrating. The silicon microtube and glass chip are bonded together and fluid enters and leaves the tube via holes drilled through the glass chip. These sensor chips are made on a wafer, with more than one hundred chips fabricated on each wafer. Like integrated circuit (IC) wafers, MEMS wafers can also be processed and tested in batches of 10- 25 wafers so that hundreds to thousands of resonators can be produced at one time.
Since the sensing element is small, much faster thermal response times are achievable with a microtube than with a one-inch to ’12-inch diameter stainless steel resonating tube. A thin-film platinum RTD has been integrated onto the microchip just a few micrometers from the vibrating silicon tube. A low thermal mass flow sensor with an attached thin-film temperature sensor is ideal for quick temperature response times.
MEMS-based Coriolis mass flow sensors have been applied to the medical field in the area of drug infusion monitoring and pumping. The Coriolis effect, which causes the tubes to twist under flowing conditions, is sensed capacitively on the microchip.
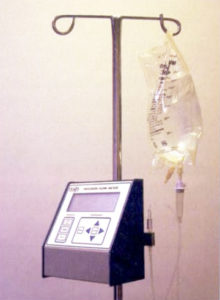
Figure 4. – Drug flow monitor using micro Coriolis mass flow sensor.
Figure 4 shows a recently FDA-approved drug flow monitor that uses such a chip to measure drug flowrates and the total volume of infused drugs into a patient in the five mUhr to 200 mUhr flowrate range. The IV line from gravity-fed IV bags are connected in series with the small flow sensor to provide an extra layer of protection to the patient and reduce the incidence of drug infusion errors. This same technology will soon find its way into the industrial flow sensor market for niche low mass flowrate applications, particularly those that need mass flow, density, and temperature readings. MEMS technology will offer industrial markets cost and size improvements and extend the lower end of fluid flowrates and volumes that can be precisely monitored.